Case Studies
Jabil Customers and Strategic Suppliers Discuss the Value Achieved Through Partnership
Filter by category
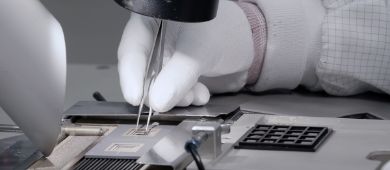
The COVID-19 pandemic brought the topic of testing to the forefront and spotlighted the need for fast-turnaround, lab quality testing that can be conducted remotely if needed. But the need for high quality, remote diagnostics also has benefits across the medical ecosystem beyond the COVID-19 era.
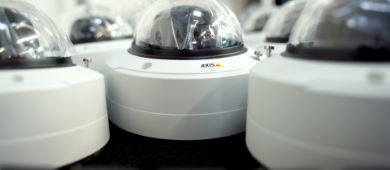
Over the past year, demand for the company’s low or no-contact access control systems grew due to COVID-19-related hygiene and social distancing concerns. Jabil was able to provide complete support for approximately 40 new product introductions and helped Axis triple production for a key customer in two months.
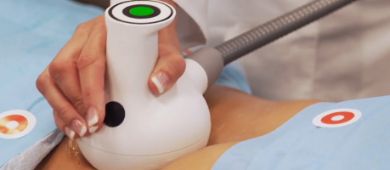
Through improvements in design, supply chain and manufacturing processes, Jabil helped usher 11 new Candela products to market in the first 18 months, while maintaining both companies’ strict quality standards. In Jabil, Candela found a partner to get them up to speed without missing a beat.
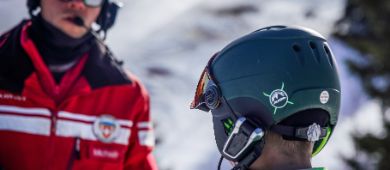
For the past decade, bike-to-bike communication has played an important part in elevating the motorcycle riding experience. Boasting an ever-growing list of innovations, “smart” motorcycle helmets now sport Bluetooth® wireless technology, mesh technology, wind-suppressing capabilities, natural language control and more.
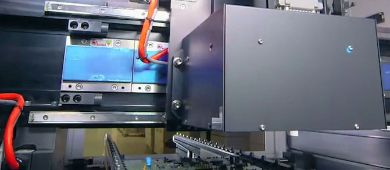
An end-to-end digital thread is critical for keeping pace with change and Digi-Key has made great advances automating its ordering process. Digi-Key also stands out for its ability to accommodate the purchase of small quantities of components when engineers are exploring new concepts or products.
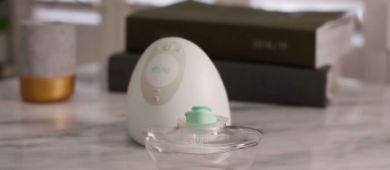
Jabil Healthcare has a unique point of view at the intersection of digital technologies, regulations, consumer behaviors and patient outcomes. This perspective proved invaluable in helping Elvie bring its groundbreaking breast pump to market.
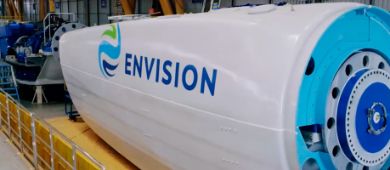
Envision’s software-defined turbine approach exceeds technological limitations of traditional wind turbines while boosting wind power generation efficiency by 15 percent. To bring their smart technology to market, Envision sought a world-class manufacturing and supply chain partner.
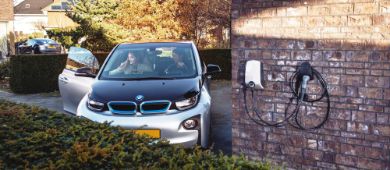
To better support continued global expansion and increased product demand, EVBox needed to elevate its supply chain and manufacturing operations — it needed a partner with deep automotive experience to ramp production to 10K units per month, and ultimately more than 200K units each year.
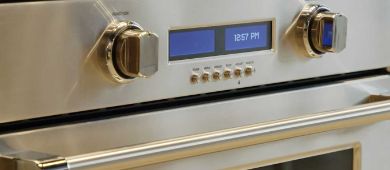
Fisher & Paykel is increasingly equipping products with embedded sensors, capacitive technologies and streamlined human-machine interfaces. To best support its burgeoning product portfolio and aggressive growth trajectory, the company decided to partner with a global manufacturing solutions provider.
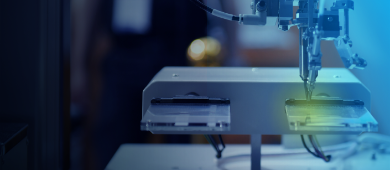
Fuji designs and manufactures the surface mount pick and place systems that are mounting the components to the circuit board itself. Fuji’s high-speed chip placers, flexible placement systems, glue stations and screen printers are unmatched in the industry for their accuracy, repeatability and durability.
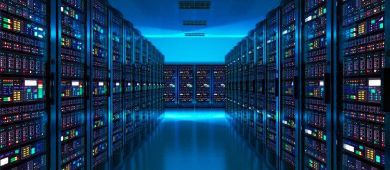
IT security is a top business priority for enterprises, government organizations and service providers around the world. However, limited visibility into data traversing physical and virtual networks, as well as public and private clouds, makes it increasingly difficult to see what’s happening across complex networks.
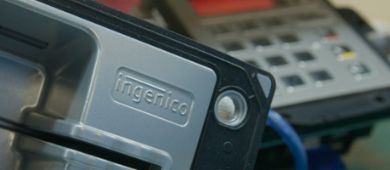
After transitioning all manufacturing to Jabil as part of its sole-source manufacturing strategy, Ingenico embarked on a major uptick in production to meet increased market demands. Ingenico also took advantage of the manufacturing consolidation to more closely integrate with Jabil’s supply chain capabilities.
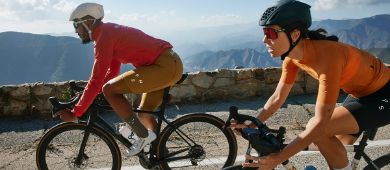
KAV, a custom helmet company, has developed an innovative way to address the demand for customization at scale. Utilizing additive manufacturing to create custom bike helmets makes KAV's production process more efficient, reducing costs and time to market.
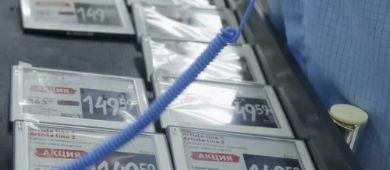
To assist with growing demand for its electronic shelf labeling solutions, SES-imagotag sought a partner with a proven track record of retail industry success. The company was impressed by Jabil’s global footprint, quality processes and ability to accommodate large-volume quantities in tight timeframes.
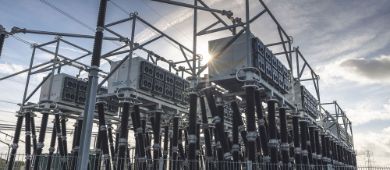
As electricity demand continues to grow, utilities must grapple with an aging grid to deliver dependable capacity — increasingly from renewables — without missing a beat. Smart Wires is championing the ability to divert electricity instantly to unused lines while enabling real-time digital control of power flows.
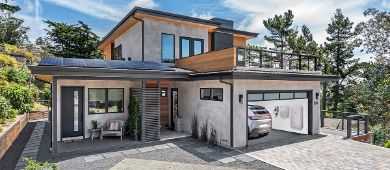
Since 2006, SolarEdge has doubled down on its efforts to change the way power is harvested and managed in photovoltaic (PV) systems. The company’s intelligent inverter and battery solutions optimize power generation while lowering the cost of energy produced by PV systems.
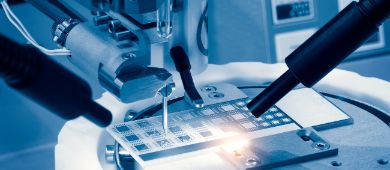
A strategic supplier to Jabil for nearly two decades, TTM Technologies focuses on volume production of technologically advanced PCBs, backplane assemblies and RF microwave components used across multiple Jabil customer sectors, markets and products.
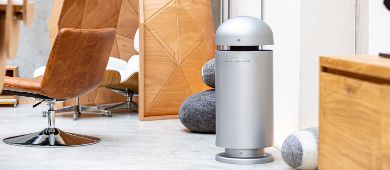
To address the growing global concerns for cleaner air and healthier environments, U-Earth partnered with Jabil to refine the functionality of their air purifier and enable large-scale production. With Jabil’s solutions, U-Earth was able to produce an effective air purifier that contributes to improving air quality and promoting healthier environments.
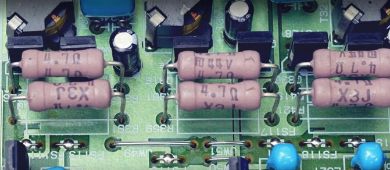
Vishay’s involvement in Jabil’s procurement and supply chain operations impacts a long list of customer markets, including automotive, industrial, power supplies, military and aerospace, consumer, computing, medical and telecommunications.
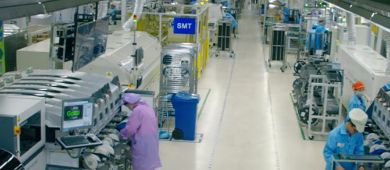
Through advanced technologies and automation, ViTrox empowers Jabil to expedite thorough inspections of highly detailed integrated printed circuit boards for any defects or imperfections. Inspection speed and throughput are essential to the performance of Jabil’s operations.
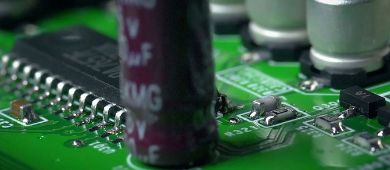
When the pandemic exposed shortcomings in supply chains and ignited sudden business disruptions, Jabil and Yageo leaned on their years of experience dealing with constrained component supplies. Yageo responded with speed and agility addressing market fluctuations caused by COVID-19.