The Rise of the Intelligent Digital Supply Chain
With numerous global market forces in play and increasing market complexity, supply chain management is at a crossroads. The pressure caused by these catalysts is reshaping the linear supply chain model into one we call the digital supply chain. In fact, digital transformation is the most complex (and critical) challenge for today’s supply chains.
Many consider Henry Ford’s automotive assembly line to be the birth of the modern supply chain, which goes something like this:
Suppliers provide the raw materials to manufacturers that pass on the finished products to distributors, which then provide select amounts of that product to the retail outlets that ultimately sell products to consumers.
This traditional supply chain model is linear, siloed and has an absolute focus on the physical movement of goods. For decades, this functional model has been refined and tweaked to support a global consumer marketplace and supply base that continues to expand. It’s been an evolution for the most part. But this old supply chain management model no longer meets today’s expanding expectations.
In the journey toward an intelligent digital supply chain, supply chain decision-makers believe emerging technologies like artificial intelligence (AI), cloud computing and the Internet of Things (IoT) will be the most impactful to their organization’s supply chain, according to a recent Jabil survey. Download the full Global Supply Chain Trends survey report.
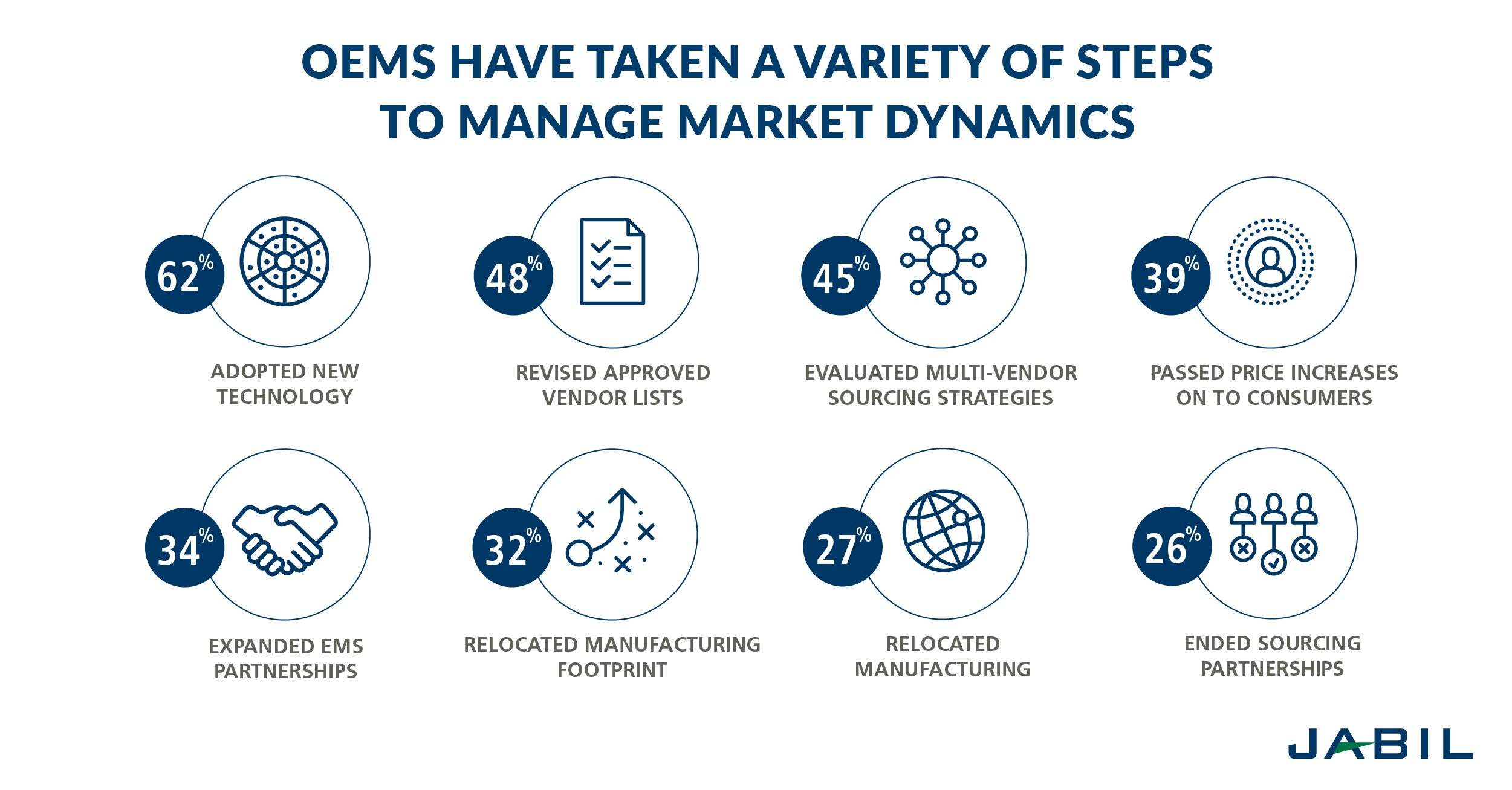
What is an Intelligent Digital Supply Chain?
Successful modern supply chain management demands real-time visibility across sourcing, transportation, manufacturing and inventory — simply put, every aspect of the supply chain. An intelligent digital supply chain leverages the cloud, real-time connectivity and advanced analytics to create a connected ecosystem.
An intelligent digital supply chain also transforms how you approach supply chain resilience and management — it requires a completely different way of working and thinking. To make it a reality, you must have:
-
Standardized data that has the same meaning and understanding across everyone involved in the process.
-
A connected ecosystem within your end-to-end supply chain.
-
Speed and intelligence that allows fidelity and real-time responses.
Traditional supply chains can at times appear dysfunctional with disaggregated sets of data, which makes the information difficult to manage. We at Jabil believe a connected ecosystem gives the customer a better experience.
In some ways, the difference between a traditional supply chain and an intelligent digital supply chain can be explained with an analogy of taxis and ridesharing applications.
The age-old problem of taxis has been that when you call one, you don’t know when it will arrive, what route it will take to reach you or how much you will need to pay. You truly don’t know what’s going on.
Ridesharing apps like Uber and Lyft have completely transformed this situation. Now you can request a car and know where it is, how long it will take to get to you, what the car looks like, who is driving it, how well the driver is rated and how much the ride will cost. Users with different smart devices can still have the same experience across operating systems and products. It makes an uncertain action easy, transparent and connected, so the consumer is always informed. That’s what we aim to do with an intelligent digital supply chain.
Two Key Steps to a Digital Supply Chain Transformation
As I mentioned earlier, going from a traditional supply chain to an intelligent digital one requires a complete transformation. In fact, MIT Sloan Management Review states that the digital transformation of the manufacturing industry is not an option. It’s critical that manufacturers do it.
“Leading a corporate transformation of any kind is difficult, and it hasn’t become any easier over time,” the article authors state. “But starting and sustaining a digital transformation in a manufacturing company? That’s tougher than managing any other change initiative.”
Digital transformation takes a long time. In most cases, the process can take five to 10 years. For manufacturers, the challenge is especially tough because the effort requires partnership across the whole value chain — including suppliers, vendors and customers.
So, where do you begin this supply chain digital transformation?
1. Establish Your Digital Supply Chain Vision
Three out of four respondents think digital supply chain transformation is important or very important, according to a study conducted by Capgemini Consulting and GT Nexus. This sentiment is echoed in Jabil’s 2018 Digital Transformation Survey of manufacturers, where 85% of respondents reported that their executives understand the criticality of and support transformation efforts.
Although your digital transformation may be a surviving or thrive effort, you need a clear vision. Why are you going to invest in this effort? Why is it important? What problems are you looking to solve?
Going digital for the sake of digital is not an answer. Companies undertaking a digital transformation effort without a vision won’t get far.
2. Articulate Your Digital Supply Chain Strategy
Once you determine your vision, it’s time to articulate your strategy. According to the Jabil survey, only 30% of respondents said they had a plan they were executed against. More than 60% are either still working on the plan or doing ad-hoc digital transformation projects.
Articulating your digital supply chain strategy happens through three components:
-
A long-term plan that outlines your journey for the next seven to 10 years and how it will be supported at all levels in the organization. This plan can also be executed on a three-year rolling basis, with updates as needed.
-
An optimization plan that outlines specific short-term goals that need to be met in order to stay in business.
-
A transformational change management plan that outlines the processes or tools you will completely change.
These components allow you to operate in two modes. One helps you focus on continuous improvement goals, like meeting or exceeding quarterly expectations. Meanwhile, the other focuses on transforming your supply chain for the future.
For example, Jabil recently undertook a transformational change to implement a more effective supply chain planning process. In four years, we were able to hook up more than 400 business units across the company and different factories. Every piece of data must be connected and making these changes in a way that works for the whole organization takes time.
It used to take our teams more than a month to analyze a customer’s forecast and give the company feedback. Now, through our revamped process, we can do it in less than a few days. Therefore, digital supply chain transformation enables the potential to do things fundamentally differently while providing a completely enhanced customer experience.
Although your journey toward a digital supply chain may require better integrated and new technologies, don’t forget that digital transformation is about people. And you must take them on the journey with you by preparing your workforce for a digital transformation.
Assessing Your Intelligent Digital Supply Chain Transformation Progress
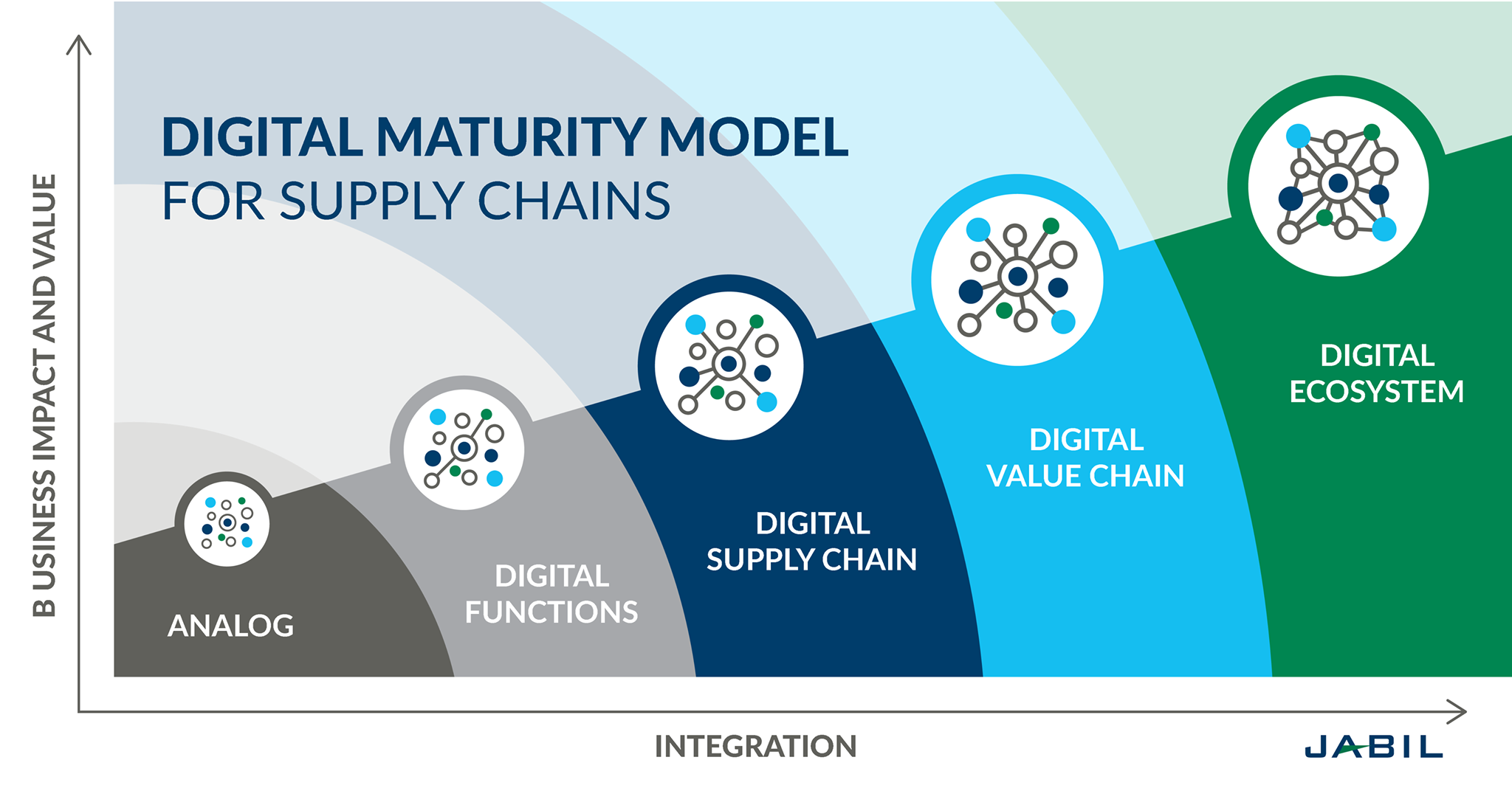
The transformation to intelligent digital supply chains is not a switch or an ultimatum. It’s not a situation of either you have an intelligent digital supply chain or you don’t. Instead, it is a spectrum with different levels of integration.
At the first or Analog stage, just about everything is done manually like in traditional supply chains. The buyer and supplier relationship in particular is governed by one-off emails, Excel spreadsheets and disconnected data. For example, if a company notices an inventory requirement for its system, the purchasing manager emails or calls the supplier to place an order, and the supplier manually responds to confirm the order and ship the item to the customer, who then manually places it in stock or on the production line. If at any point in the supply chain process the customer’s needs change, more communication and negotiation are required to ensure needs are met.
In the next stage, Digital Functions, companies are starting to digitize and automate individual functions, such as planning, sourcing, warehousing, commodity management and transportation.
In the Digital Supply Chain stage, companies are starting to link these individual, digitized, automated processes together, such as through a digital sales and operations planning platform, which merges the different types of planning related to material availability, capacity, revenue forecasting and more; a global logistics platform; or a transportation management solution.
At the Digital Value Chain level, a company has a connected value chain for at least one of its customers, linking all of the suppliers and steps that help execute a given customer’s order. Customer-specific intelligence is fed back into this value chain to optimize activities for this particular customer.
Finally, at the Digital Ecosystem level, a company has connected value chains for all of its suppliers and customers. Industry platforms and solutions help manage all of these connections, including the qualifications of each supplier, the quality of each item received or shipped and delivery information for each item. This level of digital integration offers the most seamless model and delivers the best customer experience.
Subscribe to the Jabil Blog
Sign up for weekly updates on the latest trends, research and insight in tech, IoT and the supply chain.
Barriers and Facilitators to Digital Supply Chain Maturity
The greater the level of digital integration, the higher the business impact and value. McKinsey & Company research suggests that companies that aggressively digitize their supply chains can experience 3.2% annual growth, on average, in earnings before interest and taxes as well as 2.3% annual revenue growth.
Of course, each stage unlocks a greater level of value than the previous stage, so companies do not need to feel pressured to race to the top of the integration ladder. Instead, each level of integration should be executed thoughtfully and in line with business goals. It also is important to have a digital roadmap that helps set the pace for short-term strategies and long-term investments to support digital adoption and integration.
These strategies will be critical for overcoming the barriers of technology integration and adoption. The main barriers can be classified into three categories: people, processes and technology.
As business becomes more technology-oriented, companies will need people with more advanced digital skills. As someone who began his career at a time when computers were just starting to be used in the workplace, I can tell you that it is abundantly clear that workers without digital capabilities will not be able to effectively operate in an intelligent digital supply chain ecosystem. Understanding spreadsheet programs and knowing how to manipulate data will not be enough, either. Automated programs will handle the data manipulations; humans must be able to manage the result of the technology’s work. Therefore, companies will need to invest in more training or in hiring new workers equipped with digital skills to transform the skill sets of their workforce and better support digital operations.
In line with this, workers will need to change how they complete various business processes. Going back to the buyer-supplier relationship example, intelligent digital supply chains will undoubtedly change the role of purchasing managers. Instead of handling all the procurement tasks manually, robotic process automation will handle the mundane tasks for them. In turn, the purchasing manager’s role will shift to be more managerial, requiring the manager to intervene only to handle exceptions, diagnose problems and determine the best resolutions.
On a larger scale, companies will need to be able to deploy their digital supply chain management processes globally in order to connect with each and every node in a supply chain. This will be challenging for companies that function in siloes, are decentralized and do not have shared data. Companies in these positions will first need to reorganize in order to be able to support and participate in intelligent digital supply chains.
In addition, global, digital operations will require always-on workforces that can meet supplier and customer needs on demand at any time of the day or night. Companies can fulfill this need by hiring multiple shifts to support around-the-clock operations in each factory or facility or by stationing its global workforce in different time zones around the world to deliver 24/7 service.
Technology also presents barriers on multiple fronts. For starters, new technology typically requires hefty investments. Businesses may be skeptical to put money toward technology advancements if their current systems are working, if the investments do not obviously align with business goals or if budgets already are stretched thin.
For example, the GT Nexus and Capgemini Consulting study from just three years ago found that more than half of respondents still communicated with supply chain partners through traditional technology, such as phone, fax and email. The report states that this technology situation is “fundamentally at odds with the needs of the ever-changing, fast-moving, disruption-prone nature of today’s global supply chains,” but it also shows that companies are not quick to fix systems that are not necessarily broken.
While fixing the “unbroken” may not be a priority for companies, the average supply chain leaders have also been slow to make the changes necessary to survive today’s market conditions. Only 13% of companies are fully executing a predictive supply chain risk management program at their organization today, according to Jabil’s survey. Most of the participants have not even made it beyond the process of developing their initial plan. But when we shift our focus to supply chain leaders, 96% are using predictive analytics and 85% are using prescriptive analytics to augment and automate supply chain decision-making according to Gartner.
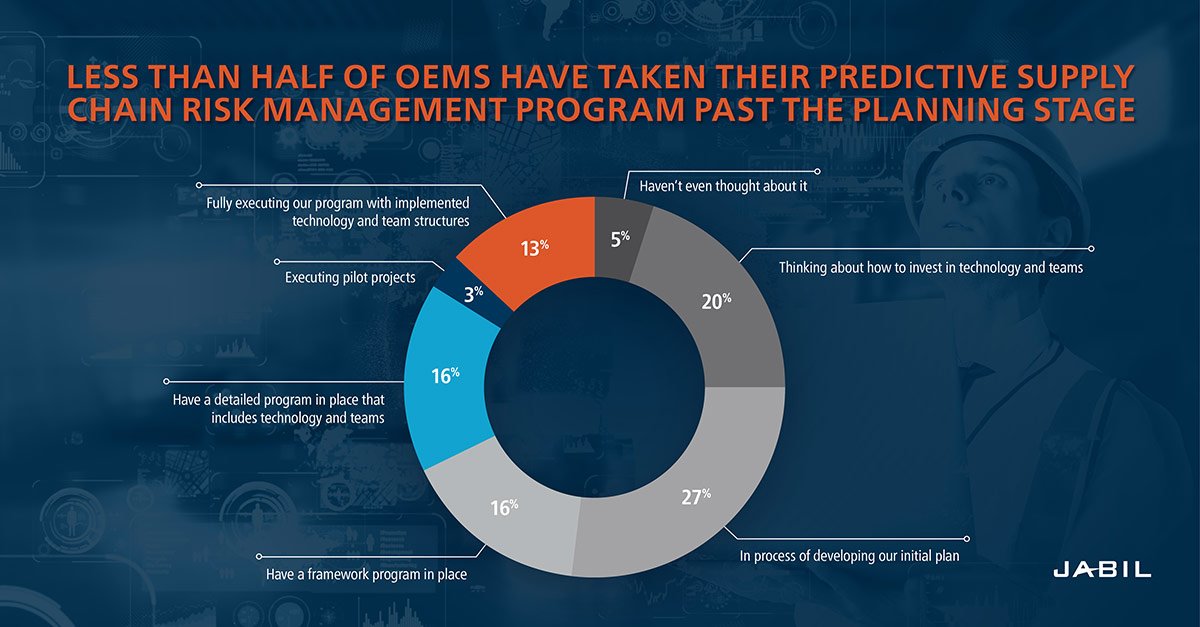
Predictive and prescriptive analytics may be a new concept to your team but their impact on the supply chain is indispensable. After all, what if your company could predict outcomes with existing data sets? What if you could then make transformational changes in those outcomes by “designing” a better performing virtual supply chain? Finally, what if you could provide game-changing recommendations into the design and sourcing decisions early in the product development cycle? All supply chains could benefit from these abilities—but these are especially important to those with longer product lifecycle products where rapid technology transitions can obsolete a product early in its life cycle.
For those companies that are investing in technology, they can be blocked by what McKinsey & Company describes as technology gaps. Essentially, advances in supply chain technologies may trail off after an initial burst of innovation. The created solutions that streamline activities, expand supply chain capabilities and enhance analytical practices can only help so much. It takes time for the technology to develop further and move a company closer to the Digital Ecosystem stage.
With the speed that technology changes, it’s important for companies to have a strong partner in information technology (IT), whether that’s an IT consultant or an in-house IT team. These professionals will help a company stay abreast of the latest technology trends, ensure the company’s IT systems are prepared to integrate with new technology and help a company use the latest technology to best advance business goals.
The Connected Future
Within the next 10 years, most if not all companies will have complete supply chain visibility from end to end. According to the GT Nexus and Capgemini Consulting report, more than half of surveyed organizations expect to have access to a majority of the data and analytics from the extended supply chain by 2021, even though only 15% of organizations had that type of access at the time of the 2016 report.
Beyond just having access to this information, most companies should be able to analyze these digital supply chain data inputs to better direct business operations and drive performance optimization. In the same report, 68% of respondents expect to be able to analyze the majority of the data from the extended supply chain by 2021, compared with 23% who were actually able to do so at the time.
At the end of the day, though, the progression toward the Digital Ecosystem stage will be used to better support customer needs. Connected supply chains and their supporting technologies, including AI, will help companies better understand consumer needs, forecast demand, manage supplies and expedite distribution to deliver on ever-changing consumer expectations. The result will be a more intelligent, digitized and automated version of Henry’s Ford’s system that might even be able to create and deliver the car of someone’s dreams quickly and with just a few clicks.
Download the Global Supply Chain Trends Report
Insights from over 300 supply chain decision-makers at OEMs with more than $500 million in revenue on how they are managing their supply chains in light of market forces.