Global Supply Chain Challenges: The Market Forces Creating Complexity
While often taken for granted when it was functioning properly, global supply chain management was already growing increasingly complex long before the COVID-19 pandemic. Now, headlines about gridlock at ports and railyards from China to Los Angeles have become mainstream topics of conversation around the globe. "Out of stock" signs have become commonplace at supermarkets, furniture retailers and home improvement stores. Behind the scenes, the global chip shortage is slowing the development of routers, switches and base stations, slowing the deployment of 5G and broadband. A lack of container ships means critical minerals used in solar panels take months, not days, to reach their destinations.
There's a shortage or disruption in every link of the supply chain these days.
It has now become obvious that one business's resilient supply chain management strategy, or lack thereof, can have enormous ramifications on many others. To the average consumer, it may not have been clear until now that the lack of a semiconductor, for example, could set off a series of slowdowns for both that product and a whole array of seemingly unrelated products.
When faced with a component shortage, suppliers must choose which companies receive those parts; OEMs not at the top of that list could be waiting a while if they have no other suppliers for that component. Finished components might then linger in a warehouse if there aren't enough container ships to get them across the ocean and on to the next step of manufacturing. The list of possible delays involving just a single component in one product is lengthy.
While these extreme disruptions won't last forever, the supply chain may never go back to the pre-pandemic "normal." According to Business Insider, retail and logistics executives are predicting that the challenges we currently face will continue through 2022. Most supply chain and logistics industry trade groups agree that we could expect to see recovery toward the end of 2022.
"Change is the only constant" seems to be a consistent mantra, but with one exception: Today it happens much faster. And the best way to win the speed game is to start before anyone else. But in order to "go faster," you need to be aware of the market dynamics changing global supply chain management.
There are three main forces driving supply chain challenges that have effects throughout the global network. In a world where every piece of the supply chain fits together to create an interconnected — albeit, at the moment, messy — picture, how do companies begin to overcome these hurdles and look to prevent future slowdowns?
COVID-19 Created Initial Supply Disruptions
The virus was the catalyst for the supply chain disruption(s) we're facing. COVID-19's impact on supply chains was felt soon after the virus began to spread in China — the source of 20% of global manufacturing — in December 2019. China quickly shut down factories and imposed a national lockdown to reduce transmission of the virus, causing significant production delays and product shortages.
In February and March 2020, those shutdowns extended to Europe, causing further delays and shortages. By April, factories in some countries, like China, were able to reopen with new safety guidelines in place, but they faced production backlogs, new levels of demand, and, most challenging of all, new logistics challenges.
Border restrictions meant to prevent travelers from bringing COVID-19 across international lines made it difficult to ship products. Then, as the number of commercial passenger flights fell drastically — first out of China and then across the world — that option for transporting components and finished products was essentially cut off. About 35% of global cargo by value is transported via commercial airliner each year, adding to the growing logistics gridlock.
This problem was compounded by the fact that most of the world's container ships were forced to sit idle and empty when the region's factories and ports shut down. There was no way for the ships to quickly or effectively move to other areas of the world that were still producing before they too were shut down. Then, when the ships that did already have goods on them arrived at ports elsewhere in the world, the ship workers were forced to quarantine on the boat.
Throughout 2020 and 2021, factories, ports and logistics operations have still faced COVID-19 outbreaks as new variants spread through different parts of the world. Groups of workers must be quarantined after exposure to the virus, or entire plants shut down if a certain percentage of employees test positive, exacerbating delays and shortages. This is a particular challenge in parts of the world that are important manufacturing hubs but have low vaccination rates — like Vietnam, which was hit hard by the delta variant in the summer of 2021.
Meanwhile, China is continuing to take strict lockdown measures when new COVID-19 outbreaks occur. Entire communities, including factories, can be shut down; quarantines at ports have caused huge backups for the overall supply chain, and the general movement of people from one place to another is limited. Truckers and container ship sailors are still subject to a wide range of testing requirements, quarantines and vaccine mandates that vary wildly from country to country. Many border restrictions are still in place, meaning some seafarers have not been, or hardly been, off their container ships since the pandemic began. The mandates, compounded by an unbelievable rise in demand, have just made logistics constraints tighter over the course of the pandemic.
Clearly, no one — not even us supply chain professionals — can plan for or control the path COVID-19 will take. But as a number of public health experts have discussed in recent months, this virus is likely not going away; it will take different forms, and we must learn to adjust. What the supply chain industry can do is, first and foremost, create working environments that prioritize the safety and health of our employees. As we've seen in the past two years, when labor is missing at multiple places along the supply chain, that chain can rapidly begin to strain and, sometimes, break.
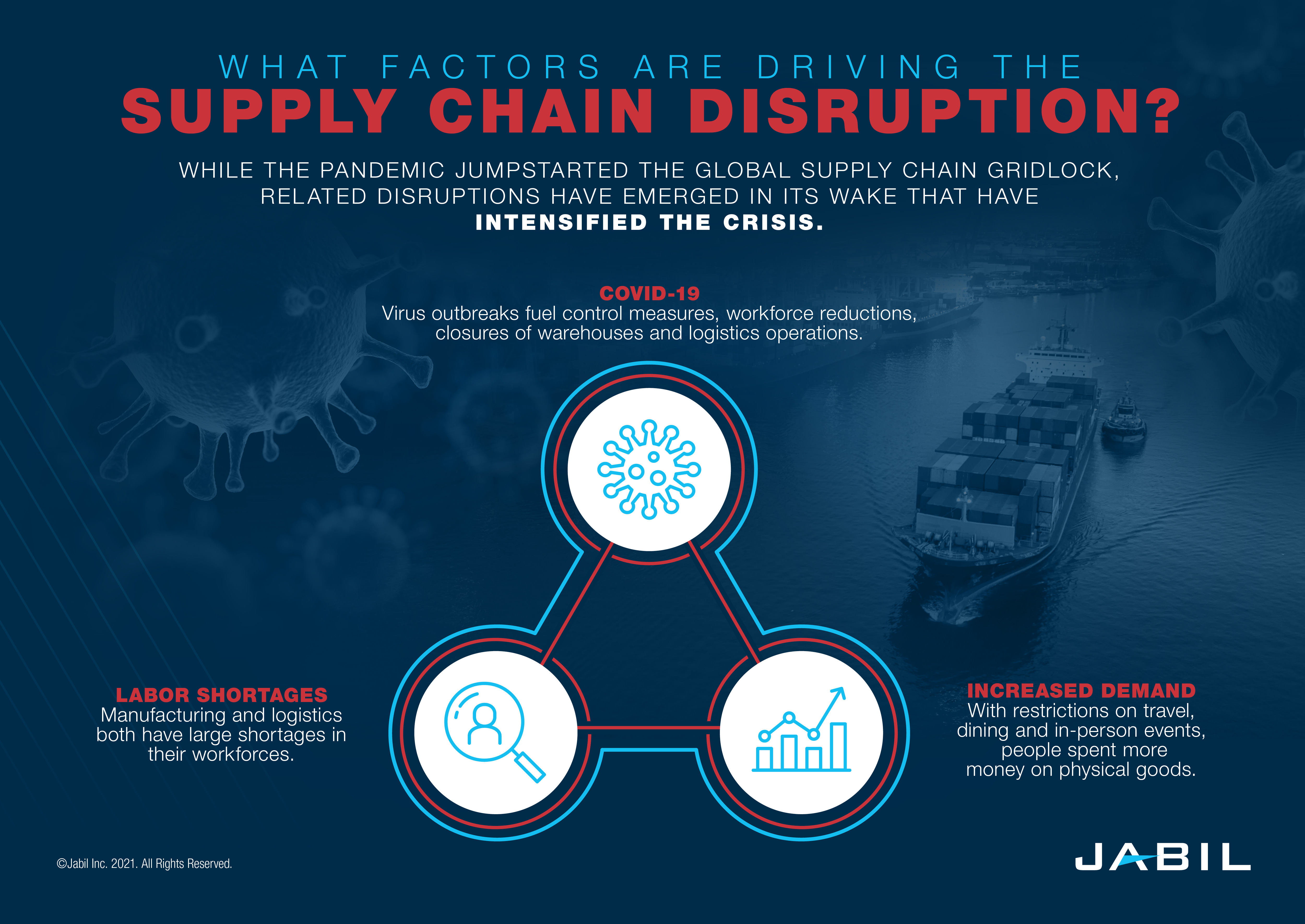
Labor Shortages Add to the Supply Backlog
Manufacturing and logistics workers may have first lost their jobs due to pandemic-induced factory shutdowns, reductions in shifts to save money or maintain social distancing, or a business closure caused by the initial economic downturn. In the United States alone, a report by Deloitte and The Manufacturing Institute found that the pandemic initially wiped out 1.4 million manufacturing jobs.
Those workers were forced to find employment elsewhere. While about 60% of those let go were eventually rehired in manufacturing, for the other 40%, factories, shipping companies and logistics operations are facing the fact that they aren't coming back — despite there being plenty of job openings.
In the U.S., 870,000 manufacturing jobs were open in August 2021, more than double the available positions before the pandemic. Deloitte and The Manufacturing Institute found that manufacturing executives' top challenges are finding the right talent (36% harder in 2021 than it was in 2018, they say) and retaining skilled talent. The executives also noted the challenge of finding the right entry-level and skilled employees in the right geographic regions for manufacturing.
This still being a pandemic, some of the labor shortage is due to employees being sick or quarantined. As the vaccine has become more available in most countries, large companies like Tyson and Ford have begun mandating vaccinations for their factory employees to help prevent spread and keep people healthy and working.
Logistics workers, like your neighborhood's package delivery person, were some of the many deemed "essential workers" during the pandemic. This segment has seen some of the biggest job growth of any industry in the past couple of years. Between February and December 2020, in the United States, the number of couriers and messengers grew more than any other profession, with warehousing and storage coming in fifth. Warehouse and logistics managers were also expected to see some of the biggest salary jumps of any fields between 2020 and 2021 thanks to the massive growth of e-commerce.
Manufacturing and logistics workers throughout the supply chain, from employees on the production lines to truck drivers, are feeling the immense pressure caused by the current unprecedented demand for goods. There are simply not enough hands and bodies in factories, warehouses, trucks, ships and railroads to keep the chain moving smoothly.
If COVID-19 lit the flame and labor shortages provided the kindling for the supply chain fire we found ourselves tending to, the upswing in demand poured on the gasoline that set the whole thing ablaze.
Increased Demand Drives Unprecedented Supply Chain Challenges
Supply chain planning happens 12 to 24 months in advance, and supply forecasts are created accordingly. In the pre-pandemic world, no one could have predicted what demand would look like today — nor could they have known to plan for the factory shutdowns that continue creating delays throughout the chain. Between catching up to backlogs and simply reacting to consumers' rapidly changing buying habits, supply is not matching the unprecedented demand.
Demand is driving supply shortages across the board more than any other factor; even the influence of COVID-19 and labor on supply lines are ultimately demand issues. Unexpected growth in demand from the consumer end likely started the bullwhip effect, where a growth in sales leads to ever-larger orders up the supply chain in an effort to stave off shortages — in turn, actually creating shortages when supply can't be passed back down the chain quickly enough. But with this crisis, the chaotic events at every level of the supply chain - from factory quarantines to truck driver shortages — are causing their own reverberations up and down the line.
Then came another unanticipated factor to influence demand: economic stimulus. As COVID-19 first spread and hundreds of millions of people worldwide lost their jobs or feared losing their jobs, spending was saved for necessities only.
Across the globe, countries quickly put money directly into the hands of consumers to spur economic growth and reverse massive, pandemic-created downfalls. While that was intended to help people pay their bills and make up for a loss of income, it also allowed people to spend more. With services and experiences like vacations and restaurants unavailable, people used that money to buy goods - putting an artificial thumb on the scale of supply and demand and creating even more strain.
The global supply chain is interconnected, with each link clicking together to help components and products travel down the line - when it's functioning normally, that is. Typically, when there's a disruption, it affects only a small piece of the chain. That piece can heal itself over with time and normal market adjustments; equilibrium is reached before too long.
Today's disastrous supply chain issues (the pandemic, hurricanes, natural gas shortages) are coupled with massive demand stimulated by economic growth. With all of these disruptions, there is an imbalance in every area, creating an unprecedented shockwave for companies trying to navigate this supply chain chaos.
Meanwhile, consumers just keep spending. According to Euromonitor International, the global economy is expected to grow around 6% in 2021, while U.S. monthly retail sales for September 2021 were up 19% over September 2019 despite rising prices (another consequence of the current supply woes). Outside of a slight dip over the summer of 2021, consumer demand, and spending, have been on a meteoric rise since April 2020.
As consumers continue adding clothing, furniture and electronics to their digital shopping carts, factories and logistics firms are working around the clock (literally) to get products to their destinations in a timely manner. But that, too, is getting more difficult by the day. As people quickly readjusted to new ways of living and working after the realities of COVID-19 set in, the shape of that demand changed drastically. Supply chain management must change as well to keep up.
An Increasingly Disrupted World
A pandemic the size of COVID-19 is a once-in-a-generation event. While we will learn to live with and manage this particular virus, there will be many more disruptions to the supply chain, and possibly our day-to-day lives, in the years to come.
Disruptions in the component supply chain existed well before the pandemic thanks to the rapid expansion of connected devices across industries like healthcare and automotive and the aging out of older components putting pressure on supply. Then, the shift to remote work, school and ramp in demand for IoT devices that helped reduce person-to-person contact at businesses fueled shortages that had just recently been cleared dating back to 2017 and 2018.
Component shortages — especially of semiconductors, vital to every electronic and IoT device — will perhaps take the longest to clear. Large chip designers and manufacturers have acknowledged that the problems could extend well into 2023 and beyond. These shortages have massive ramifications down the supply chain. Despite high demand, auto manufacturers are cutting their production goals because they simply don't have the semiconductors they need. Even medtech companies are seeing delays and cancellations of their chip orders.
The world is volatile; that won't change. Even as COVID-19 outbreaks slow down, the labor force is rebuilt and demand levels off, shortages will still exist in the component market. The takeaway is that companies must design a supply chain that can respond to this volatility, investing in capabilities to manage supply networks when they become disrupted by natural disasters, public health emergencies or geopolitical events.
Amid Today's Market Dynamics, Speed and Tenacity Matter
Even without the market forces we've discussed, global supply chain management is complex enough. In an effort to manage supply chain risk around market forces, OEMs have taken a number of steps in the past few years to adjust their supply chain strategy:
- Adopted new technology
- Revised approved vendor lists
- Evaluated multivendor sourcing strategies
- Passed on price increases to consumers
- Expanded EMS partnerships
- Relocated manufacturing
- Ended sourcing partnerships
- Invested in lobbying to influence policy
- Eliminated markets
Although these tactics represent diverse options across the supply chain landscape, adopting new digital platforms leads the pack. But as an industry, we must be careful in the selections we make. I see many companies spending their money on "digital" solutions without properly identifying the problem to solve.
Ayman Omar, an associate professor specializing in global supply chain at American University's Kogod School of Business, points out in a recent Los Angeles Times article that the main problem is a lack of transparency within the supply chain. Manufacturers, importers, logistics companies and other players along the chain are never quite sure where components or products are at any given time, making it impossible to see problems in advance and get ahead of them.
New digital solutions, then, are vital for enhancing the visibility and traceability of each piece of the supply line, eliminating the mysteries that currently exist within it.
Visibility and Predictive Analytics in the Supply Chain
The supply chain of the past is not the supply network of the future. To effectively manage this new network, companies must be able to see each part of it — from factory inventories to the availability of tier 2 and tier 3 suppliers and the status of products as they travel across skies and oceans. A visible supply chain requires a detailed knowledge of each element of a product's manufacturing, lead time, inventory and more.
Transparency helps answer questions like: Where is this specific part I need? Is it in transit? Is it sitting in a warehouse across the ocean? However, it's only part of the equation. While you can react once you know who has which part where, you can't get ahead of a problem at that point. For that, you need predictive analytics.
Investing in cloud-based digital order management solutions provides visibility into the entire supply network. But investing in a truly intelligent digital supply chain solution involves data and modeling to evaluate all types of risk at each piece of your supply network, as well as creating lifecycle curves to create technology roadmaps for your products. The pandemic has taught us new metrics to take into consideration when evaluating risk, like health and safety plans, government influence and the labor market.
A combination of visibility and data gives companies the ability to make decisions that are scalable and predictive — so you can get ahead of the next crisis. Finding a partner that can manage both this new digital infrastructure and your entire supply chain, from cradle to grave, is one way to mitigate the risk inherent in this increasingly complex global supply network.
A Partner to Orchestrate the Supply Chain
In order to see where a component within the supply chain and analyze its place within the product's lifecycle, you first need someone to set the chain in motion and direct it as it begins to operate. A partner with supply chain expertise can help guide companies to build supply chain resilience that provides customers the products they need when they need them.
It is imperative to note that, in our current supply ecosystem, there are no quick fixes. Partners like Jabil can develop a solution for the future — in the hopes of circumventing the next disruption. With predictive analytics, supply chain partners can help determine which risk mitigation solutions, like regionalization or multiple suppliers, are best for creating a resilient supply chain. They also have the ability to build relationships with and gather data from suppliers and other partners within the supply network — an invaluable asset for any company's supply chain.
Still, the only guaranteed solution to untying the knot that is the global supply network is time. Driven primarily by the triplet forces of COVID-19, labor issues and unprecedented demand and their trickle-down effects, the supply chain challenges will run themselves out and equilibrium will be reached — eventually.
For companies attempting to navigate this web, true end-to-end visibility, actionable analytics and hands-on management of their entire chain are crucial to making agile, proactive decisions before an acute crisis strikes. By creating their own connected supply network within the global ecosystem, companies and their partners can foresee challenges and overcome them before they arise.