The Future of Supply Chain Management is Risk Management
Throughout history, there are moments that force change. The 2020s have brought multiple, like the COVID-19 pandemic and its resulting component shortages, conflict in Ukraine and the Middle East, and increasing geopolitical tensions. The interlocking impacts of these disruptions reveal that the future of supply chain is all about proactive risk management.
Jabil’s 2024 Supply Chain Resilience survey — conducted by SIS International Research — examined the current strategies and long-term goals of nearly 200 supply chain and procurement decision-makers around the world. The survey found that companies have struggled to meet their business or operational goals in the past year due to the far-reaching impacts of disruptions. More than eight in 10 respondents (84%) have dealt with component or material shortages, three quarters have seen delays in their time-to-market, and two thirds (67%) have faced complications in their supply chain and procurement processes from geopolitical factors.
To effectively manage this new kind of supply chain, risk mitigation is a key area of improvement for supply chain and procurement organizations. Nearly half (49%) of survey respondents said enhancing risk mitigation and flexibility is a main goal of their procurement organizations, while 38% are focused on increasing adaptability and flexibility in their supply chain organizations.
How Are Companies Preparing their Supply Chain for the Future?
Think back to 2020: As COVID-19 spread internationally, the resulting disruptions caused many supply chain organizations’ strategies — from sourcing to logistics — to break under the pressure.
Now, risk mitigation is a key consideration in supply chain management. What risk mitigation looks like, and the tools and processes used to facilitate it, are different at every company. Organizations must identify their pain points and top risk factors — both internal and external — and put plans into place to overcome those challenges and lower their exposure to risk.
At Jabil, we support over 400 customers and manage 36,000 suppliers each day. Our team has learned that building a supply chain to withstand challenges is not “one-strategy-fixes-all"; multiple layers of mitigation provide the best chance at continuity in the face of disruption. Here are five ways we see companies center risk mitigation in supply chain management to navigate an increasingly complex world.
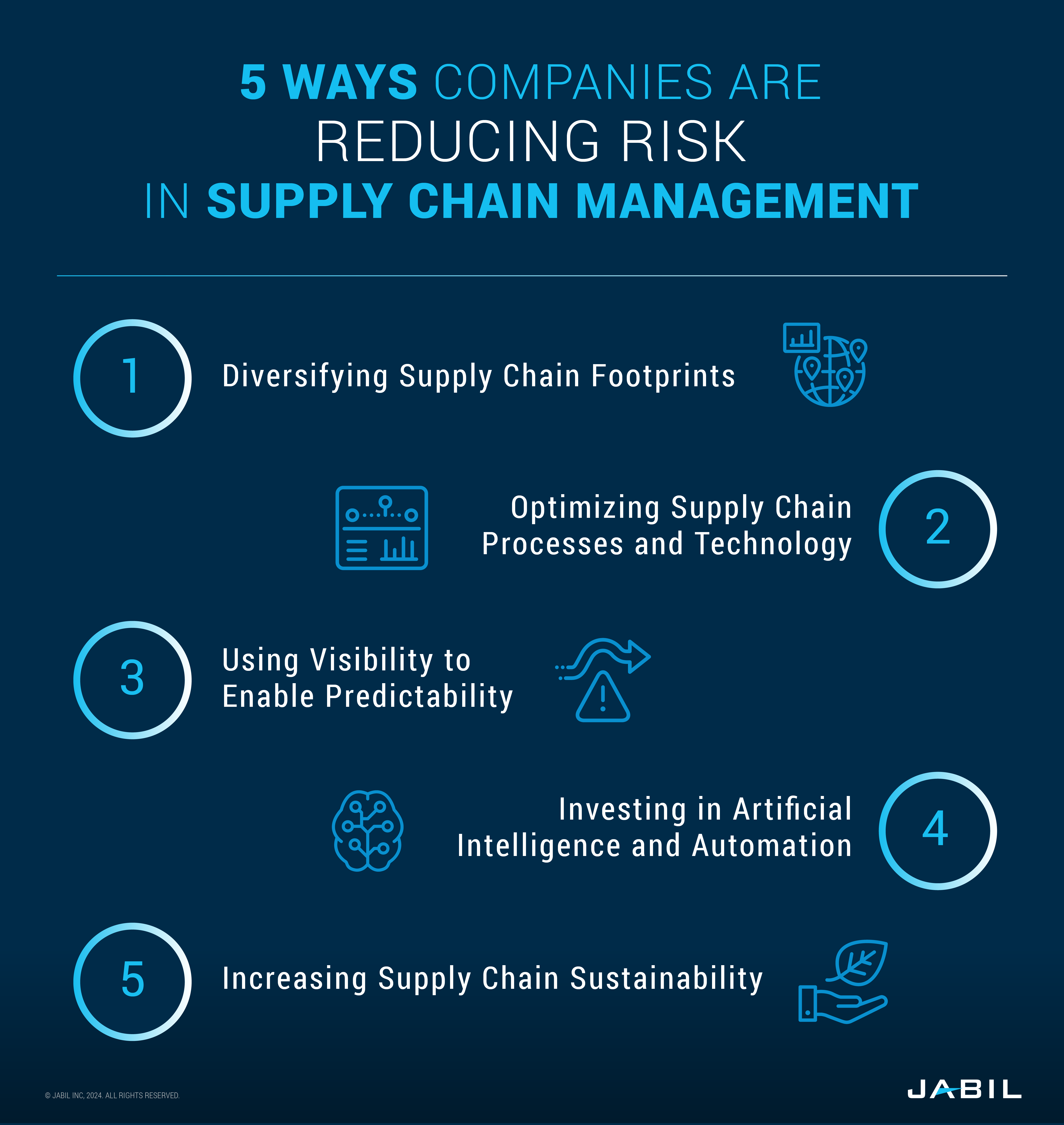
1. Businesses Are Diversifying Their Supply Chain Footprint
After COVID-19 started spreading, people began wondering if companies would start moving away from China. The pandemic created fear that companies may be too reliant on China for everything from the key ingredients used to make cleaning agents to pharmaceuticals and personal protection equipment (PPE). It was alarming when the country shut down and we all realized how dependent the globe is on supplies and workers located in China.
China is and will likely remain a major global manufacturer. However, the issue has become more complicated since 2020. Government initiatives like the U.S. Inflation Reduction Act, CHIPS and Science Act, and the European Commission’s Made in Europe partnership are incentivizing or legislating companies to relocate part or even all of their manufacturing and supply chains domestically. In addition, corporate sustainability goals increasingly being part of sourcing decisions is accelerating the movement of production to be nearer the point of consumer consumption. China is facing these challenges in addition to rising labor costs and U.S. tariffs. Geopolitical tensions between the two countries are also leading companies to seek production bases elsewhere.
Because of the modern supply chain’s complexity, it is unlikely that many companies will make the decision — or even have the capability — to move their supply chains out of China completely. However, we’re seeing more and more companies maintain a presence in China while building out a supply chain in at least one other region — a diversification strategy often called “China +1.” Nearly two thirds of survey respondents (63%) said they have a supply chain strategy outside of China, while 10% are working to develop one.
Companies that have or are building a China +1 strategy are largely localizing their supply chain activities in three regions: Southeast Asia (61% of respondents), the U.S. and Canada (44%), and Western Europe (33%). This strategy is most prevalent among companies in the consumer electronics, smart home, cloud, healthcare, and energy and industrial industries, likely speaking to their desired end-markets.
Relocating all or even just some of a supply chain is a tall order for even the most sophisticated organizations. Working with a strategic partner who can tap into their developed supplier and logistics across the globe is one way for companies to ease the transition to new regions while maintaining continuity for both internal teams and customers.
2. Supply Chain Process and Technology Optimization Remains a Strategic Priority
In this era of disruptions, having efficient, resilient, optimized supply chain processes are perhaps even more critical than they were pre-pandemic.
Optimizing for resiliency is a strategic priority for 82% of respondents, underlining the importance of supply chain resilience in risk mitigation. Interestingly, the most disagreement on this sentiment came from the telecommunications sector. One fifth (20%) of respondents from organization in this industry chose “strongly disagree.” This group represented a small sample size, but its views could be reflective of the current economic headwinds the industry faces.
Building a customized technology stack is one of the most effective strategies for supply chain and procurement organizations looking to optimize their processes. Nearly all (93%) survey respondents said the supply chain and procurement technologies their company is leveraging are providing measurable results, like improved efficiency, cost reduction, or other benefits.
However, this message doesn’t seem to be making it to the top of the org chart. Survey respondents in leadership roles were the most likely to say their organization is not seeing results from technology. One fifth of VPs and one fourth of C-suite executives said they are seeing few to no results from supply chain technologies.
At some organizations, there seems to be a critical lack of communication between the teams working hands-on with supply chain technology and their leadership. Only 50% of decision-makers said their supply chain organization has received investment from the executive or C-suite level to support their optimization strategies. For C-suites to continue investing in supply chain and procurement organizations, they need their teams to deliver the ROI; for teams tasked with delivering the ROI, they need the time, trust, and resources to not only implement new tools but also use them to make data-driven decisions.
3. Organizations Will Use Visibility to Enable Predictability in the Supply Chain
Lots of people tout the virtues of a fully visible supply chain. Almost half (46%) of survey respondents said enhancing visibility and communication across the value chain is a main goal of their supply chain organization over the next 12 to 24 months.
Make no mistake, visibility is very important. It can help you maintain up-to-date knowledge about your inventory management and supply chain operations, improve performance, and reduce errors. However, visibility alone doesn't enable organizations to be proactive.
Supply chains need predictive, actionable intelligence to essentially create visibility into the future. It allows us to build answers to problems that are highly likely to occur and lay the groundwork for strategic planning ahead of disruption.
Having visibility of today's problems is too late, and many organizations don’t even have that. Nearly seven in 10 (69%) of decision-makers said they have limited visibility into the product lifecycle and need more; only 22% say they have complete visibility into the product lifecycle.
The goal is to create visibility into the future with predictive modeling of supply chains. At all times, we must be able to evaluate the current situation using advanced analytics. Once we're past the crisis, we can determine how fast we responded and how long it took to recover and thrive.
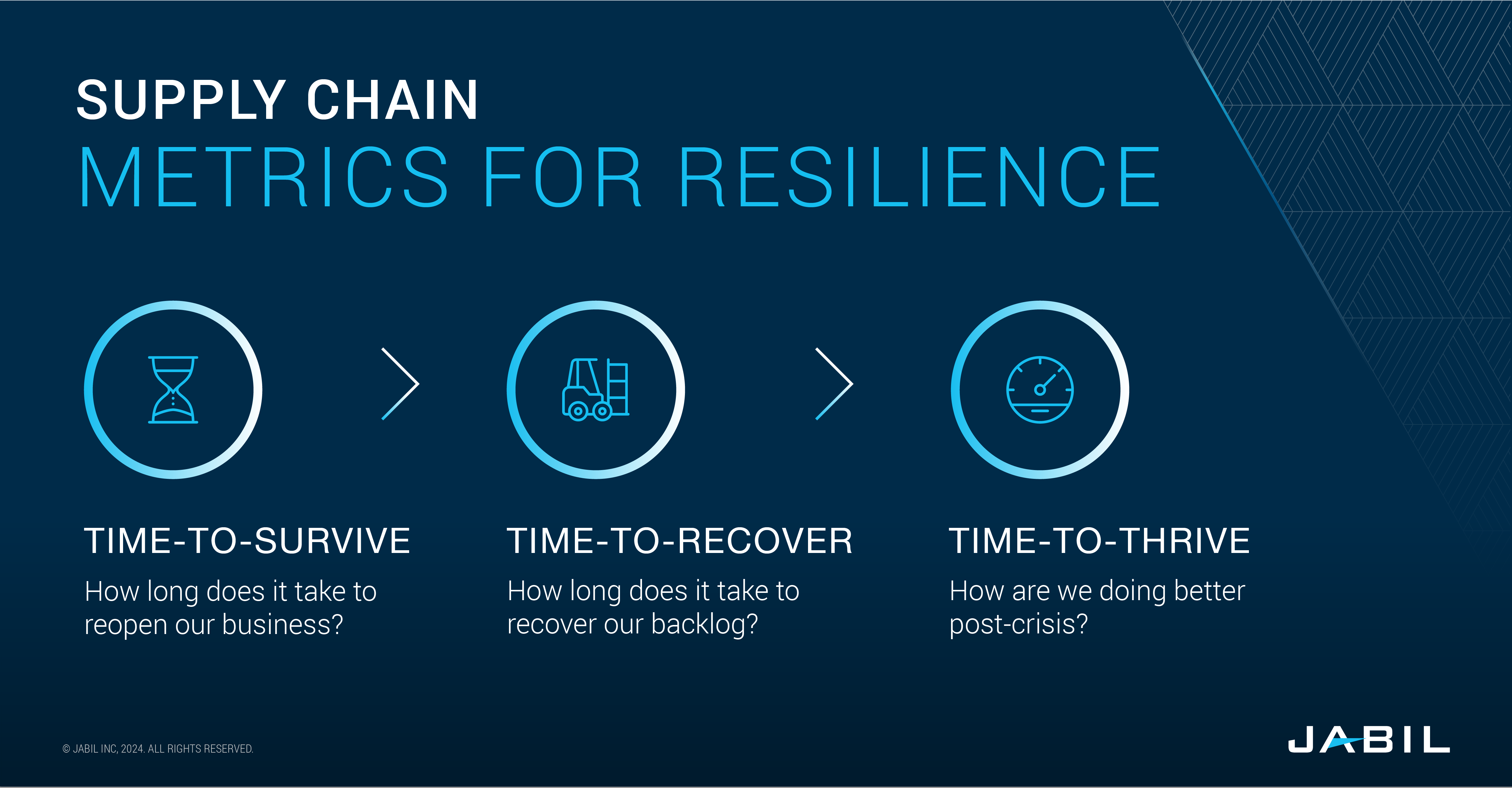
Market intelligence — made up of expertise from practitioners along with data and analytics — plays a crucial role in making informed supply chain and procurement decisions in both the short and long term. From determining availability of supply to tracking pricing trends and slowdowns in logistics modes, nearly all (96%) surveyed decision-makers are using market intelligence to some degree in their supply chain and procurement decisions. However, roughly half of those organizations (51% of respondents) said they need more market intelligence than what they have currently to accurately assess opportunity and risk.
The key to actionable visibility is gathering usable data. The supply chain has continued to be reactionary because people moved on from past challenges too quickly, thinking that the problem was solved — until the next crisis.
Now, with the significant changes in how we live and learn, we are realizing that managing the supply chain is not primarily about how well you can react; it's about how predictive you can be. It seems companies are taking this to heart, as two thirds (66%) of survey respondents said they are using predictive analytics and artificial intelligence or machine learning models to make strategic decisions about their supply chain activities.
The problem is that the language of supply chain risk mitigation tends to focus on increasing agility and flexibility. While these are still important characteristics of a resilient supply chain, they speak to reactivity — not proactivity the way predictability does. Maybe because you need data to predict. And the more specific and higher quality the data, the better the solution.
Supply chain professionals need to shift the conversation from how we can best respond to problems to how we can prevent problems in the first place. Predictive supply chain modeling will create faster, less expensive supply chains — and it’s increasingly relying on AI.
4. Investments in Artificial Intelligence and Automation Will Increase
Automation and AI are already commonplace in the production piece of supply chains, enabling predictive manufacturing to prevent mistakes on the line before they happen.
As I briefly mentioned earlier, we’re seeing a rapid adoption of AI and machine learning (ML) for predictive supply chain management. However, this evolution to Industry 5.0 emphasizes having people at the center of the work; automation is not a replacement of, but rather a partnership with, skilled workers. Moving forward, expect to see routine tasks and tasks that require complex calculations become digital at a more aggressive rate. We could also see the adoption of generative AI to help parse the vast amounts of commodity and category data that supply chain organizations gather on a daily, weekly, and yearly basis.
Survey respondents indicated that they use AI and ML for some of these tasks already:
The supply chain use cases for AI and ML are exploding, and it’s quickly becoming clear that the technologies can make a positive impact on organizations’ top pain points, including visibility, efficiency, and cost. Some of the biggest effects that supply chain decision-makers anticipate from AI and ML include:
- Increased visibility into the entire supply chain (76%)
- Reduced labor costs through increased automation and efficiency (70%)
- Increased accuracy in the demand planning/S&OP process (64%)
- Improved procurement efficiency (62%)
- More effective risk management strategies via real-time insights into potential supply chain disruptions (58%)
Artificial intelligence is advancing at a breakneck pace. To keep up, supply chain organizations must have an established data governance strategy to ensure the information being fed to AI models is uniform and coherent across teams and sites. Structured data streams will allow AI to make systems more efficient and predictable — not only for today's environment but, more importantly, for tomorrow's disruptions.
5. Supply Chains Will Become More Sustainable
In the chaos of the past few years, the hyper-focus on getting customers their orders on time at the lowest possible cost has left sustainability a bit lost in the shuffle. But not anymore.
An increasing number of regulations meant to reduce greenhouse gas emissions are creating new challenges for the global supply chain. Logistics is bearing the brunt of these changes, particularly in Europe. Between 2023 and 2025, the European Union is rolling out new sustainability requirements that impact nearly all logistics modes on the continent.
Beginning in 2025, the ReFuelEU law will mandate that all flights departing from an EU airport must use some amount of sustainable aviation fuel (SAF) — a minimum of 2% in 2025, 6% in 2030, and 70% by 2050. SAF is already more expensive than traditional fuel, and there are concerns that additional demand could force the price even higher.
On the seas, the EU's Emissions Trading System (ETS) — in which companies must buy allowances to emit greenhouse gases or pay heavy fines — began including CO2 emissions from maritime transport within EU waters and for voyages from EU ports on January 1, 2024. Our internal projections show that this could drive up 2024 costs by 30% over 2019 (pre-pandemic baseline).
Finally, Europe’s forwarders and road freight operators are warning customers to expect a significant increase in toll fees. A new European toll system linked to CO2 emissions was rolled out in Germany in December 2023 and will spread to the rest of the EU by March 2025. Rates are dependent on vehicle weight, and thus how much CO2 the vehicle emits. Toll payment solutions provider DKV Mobility estimated forwarders would pay a surcharge of €200 per ton of CO2 on all commercial vehicles over 7.5 tons. In Germany alone, this is estimated to increase costs for the trucking industry by 83%.
Across the board, logistics providers will need to pass these costs on to their customers. We anticipate similar ESG regulations will start to go into effect across the U.S. in the next few years, making sustainability of products and supply chains a priority for the global supply chain.
Our survey respondents indicated that supply chain organizations are already making shifts to reduce their environmental impact — recognizing that sustainability and resiliency go hand in hand. Nearly eight in 10 (79%) of respondents said their organizations have developed processes to reduce waste and energy consumption throughout the supply chain. Other respondents have focused their sustainability efforts more on procurement, with 74% establishing sustainable procurement policies for suppliers and 68% sourcing materials and components from validated sustainable suppliers.
However, with regulations still in their early stages, sustainability isn’t necessarily a high-priority goal for supply chain and procurement organizations yet. Only 8% of respondents said a reduction in environmental impact associated with the organization's supply chain activities (i.e., Scope 3 emissions) is a measure of success of its long-term supply chain optimization goals. I wouldn’t be surprised to see this number grow as more countries implement their own laws regulating companies’ carbon emissions, water usage, and waste generation.
Strategic partners like Jabil can help organizations set and work toward their sustainability goals as part of an overall optimization. Roughly half of respondents have considered or would consider outsourcing some element of their supply chain and procurement activities to an external partner. On the low end, 46% said they would or have considered outsourcing procurement management; on the high end, 80% would outsource logistics. A partner with specialized expertise in some or all areas of supply chain and procurement can help organizations assess and advise which tools and solutions will work best to monitor their sustainability progress and mitigate risk.
The supply chain process has been forever altered by the disruptions of the past half-decade. The pandemic served as a wake-up call to supply chain executives as they use these challenging times as an impetus for something much greater: the future of supply chain. Begin by building a more resilient supply chain and thus a stronger business strategy.