CP150 Series Automation System
Flexible, High-Precision Automation Systems
The CP150 automation platform delivers future-proof flexibility to any production line by delivering a highly-modular, scalable system that addresses a variety of automation needs.
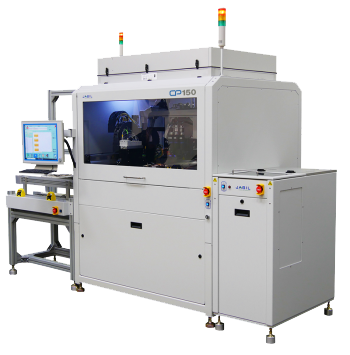
Enhanced Capabilities
Metrology
We design and deliver non-contact metrology solutions that increase production throughput and repeatability.
-
Ability to identify cosmetic defects, coating thickness, gaps, and offsets
-
High-speed multi-angle light triggering
-
Custom AI Defect generation software
Optical Inspection
Our inspection capabilities allow you to identify and measure micron-level defects and surface flaws to ensure your products maintain the highest standards of quality.
- Cosmetic Defects
- Coating Defects
- Surface Finishes
- Gaps and Offsets
- Color and Gloss
Lamination
The ability to align, place, and cure our lamination capabilities delivers a streamlined process in your manufacturing processes.
- Alignment repeatability within 10 microns
- Scaleable for a variety of rigid and flexible material combinations
- Non-contact “Bernoulli End-Effector” loading and unloading of materials
- Automatic Planarity Adjustment
High-Speed Final Assembly
When it comes to high-speed, high-precision assembly we deliver robust capabilities designed to help you achieve your manufacturing goals.
- Label Placement
- Point-to-Point Soldering
- Precision Dispensing
- High-Speed Pick and Place
- Vision-Based Alignment
- Robotic Screw Fastening
Key Benefits
High Flexibility
The CP Series allows for a variety of configurations that can support any number of interrelated processes, production speeds, and quality levels. Configure pallet or edge-belt conveyors with either a reversible left-to-right or right-to-left conveyor flow to optimize your manufacturing processes.
Multiple Levels of Automation
The platform supports a wide range of processes, ranging from semi-automatic to fully automated modes, to help support your manufacturing objectives.
Redeployable
Future proof your investment by re-deploying the CP Series work cell for various applications. Common interfaces enable rapid change-over of applications; saving you time and money.
Key Features
- Platforms can be configured in any orientation ensuring optimal support of interrelated processes, production speeds, and quality levels
- Modular Z-axis and Theta axis (optional) available
- Multiple Vision location options (up-camera or down-camera)
- Standardized mounting flanges and control interfaces
- Quick-change feeder mounting available
- OSHA and ANSI compliant
CP150 Specifications |
|
---|---|
Machine Footprint |
|
Work Envelope |
|
Axes of Motion |
|
Z Max. Stroke |
|
Theta |
|
Manipulator Payload |
|
Manipulator Repeatability |
|
Utility Requirements |
|
Product Presentation |
|
Feeder Slots Available |
|
Electrical I/O |
|
Pneumatic |
|
MES Connectivity |
|
Controls |
|
SIM500 Series Automation System
A Flexible, Cost-Effective Automation System
Jabil’s Standard Integration Module (SIM) platform utilizes interchangeable modules to automate basic to complex production applications. Pre-engineered solutions minimize risks, simplify integration, and reduce lead-time. SIM platforms can be used inline or as stand-alone workstations.
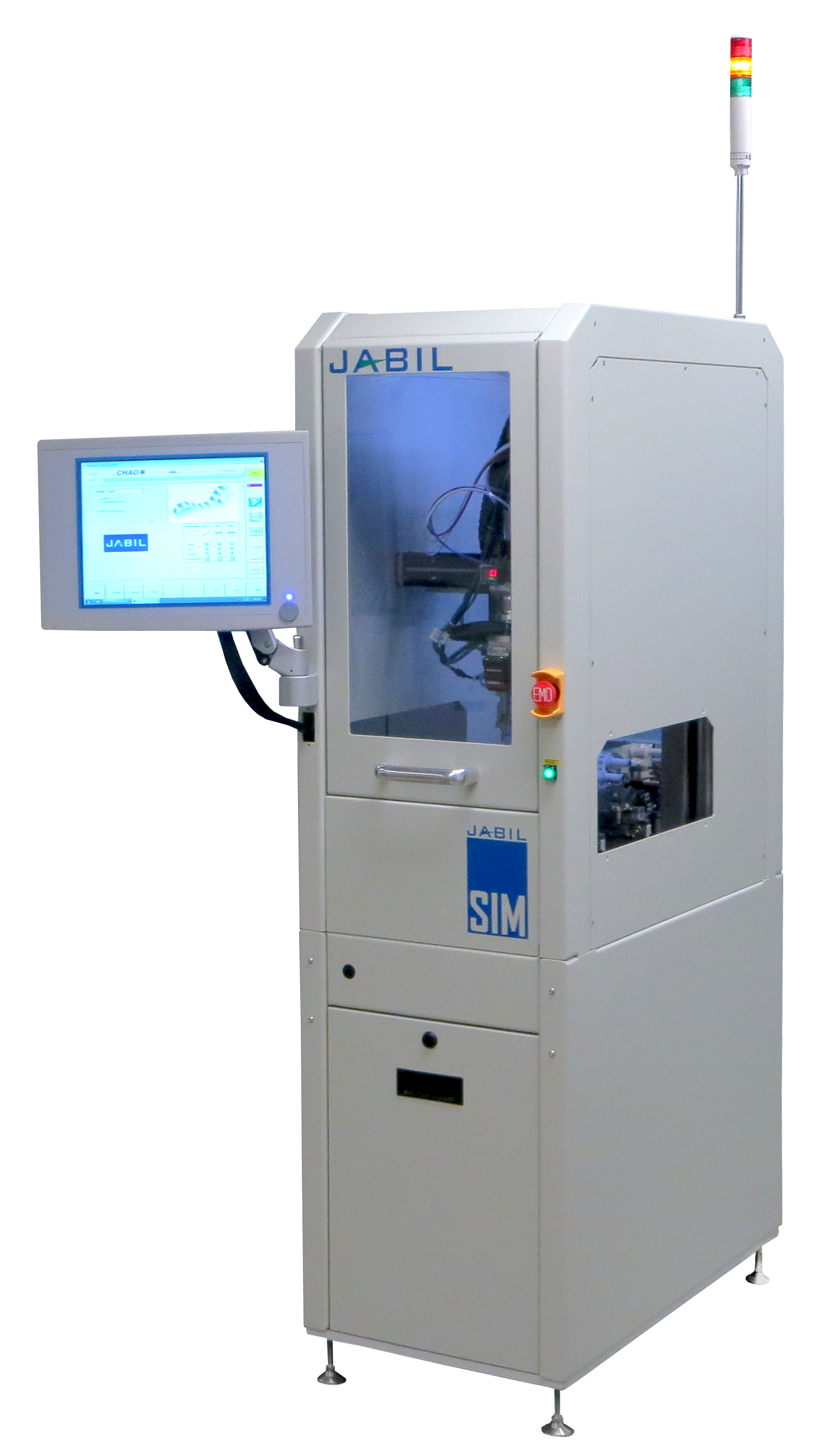
Key Capabilities
-
Pick and Place
-
P2P Soldering
-
Screw Fastening
-
Label Placement
-
Vision-Based Alignment
-
Precision Dispensing
Key Features
-
The SIM is a re-deployable system featuring common interfaces that enable rapid change-over of applications
-
The platform supports a range of processes from semi-manual to fully automated
-
The platform can be fitted with a pallet conveyor or edge belt conveyor, with reversible left-to-right or right-to-left conveyor flow
-
Platforms can be configured in any orientation ensuring optimal support of interrelated processes, production speeds, and quality
-
Modular Z-axis and optional Theta axis
-
Vision location options (up-camera or down-camera)
-
Standardized mounting flanges and control interfaces
-
Quick-change feeder mounting
-
Full safety guarding (OSHA and ANSI compliant)
Equipment Options
- XYZ Cartesian
- Edge Belt or Pallet Conveyor
- Pneumatic Shuttle (future)
- Board Support (tall stroke)
-
Theta Axis on Manipulator
-
Vision Up-Camera or Down Camera
-
Barcode Reader
SIM500 Specifications
|
|
---|---|
Machine Footprint
|
|
Work Envelope
|
|
Axes of Motion
|
|
Z Max. Stroke
|
|
Theta
|
|
Manipulator Payload
|
|
Manipulator Repeatability
|
|
Utility Requirements
|
|
Product Presentation
|
|
Feeder Slots Available
|
|
Electrical I/O
|
|
Pneumatic
|
|
MES Connectivity
|
|
Controls
|
|
IQPS Series Automation System
A Flexible, Cost-Effective Odd-Form Automation System
The IQps™ is a low-cost automation platform that offers an ideal solution for Odd Form Pick-and-Place and other circuit assembly applications. Easy-to-use motion and vision controls provide excellent capabilities. Standard assembly tools provide great system flexibility. Fully configurable, the IQps™ is an excellent choice for standard and custom odd form applications.
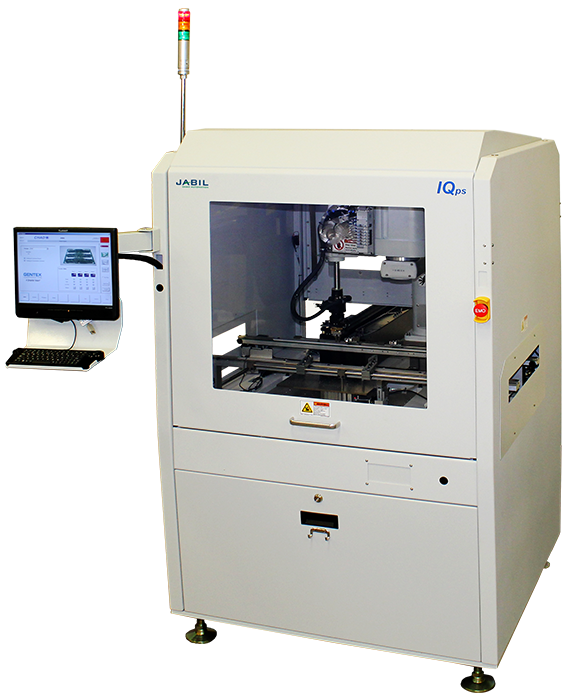
Key Features
-
Active or programmable lead clinch
-
Ability to handle virtually all component types
-
Quick-change feeder slots
-
Edge belt conveyor with board stop and board locating tooling
-
EPSON 4-axis SCARA Robot with motion controller
-
Simple, intuitive IQware™ application software
- EPSON 4-axis SCARA Robot with motion controller
- Simple-to-use IQware™ application software and intuitive operator interface, via Windows PC and manual control pendant
- Edge belt conveyor with board stop and board locating tooling, as well as board support
- Active or Programmable Lead clinch (optional)
- Quick-change feeder slots accept all standard part feeders. Options for 4, 6, or 10 feeders
- Compatible with standard CHAD Grippers, including standard mechanical and vacuum grippers, plus the CHAD PIE™ compliant gripper
- Ability to handle virtually all component types, including axials, radials, pin headers, capacitors, connectors, transformers, relays, TO-220’s, displays, LED’s and more
- Custom specifications can be accommodated
- Full safety guarding (OSHA and ANSI compliant)
System Options
- Active Clinch Heads
- Programmable Single Pin Clinch
- 3-Section Conveyor
- Auto-Width Conveyor
- Vision Board Location or Part Location
- Bar Code Reader
- Product Traceability Options
Grippers
- SGE Single Grip End Effector (mechanical or vacuum)
- MGE Multi-Grip End Effector
- PIE 3D Compliant “Floating” Gripper
Feeders
- RC Radial Tape Feeder
- AF Axial Tape Feeder
- TM Tube Magazine Feeder
- Bowl & Inline Feeder
- Tray Feeder
WaferMate 300 Series Wafer Handling System
High-Performance Wafer Handling Automation Systems
The WaferMate300 is a highly configurable, BOLTS-compatible robotic wafer-handling platform that mates high performance with cost competitiveness. As an ISO Class-2 clean EFEM, this platform includes all applicable mini-environment components, E84 compliance, and rear hand-off.
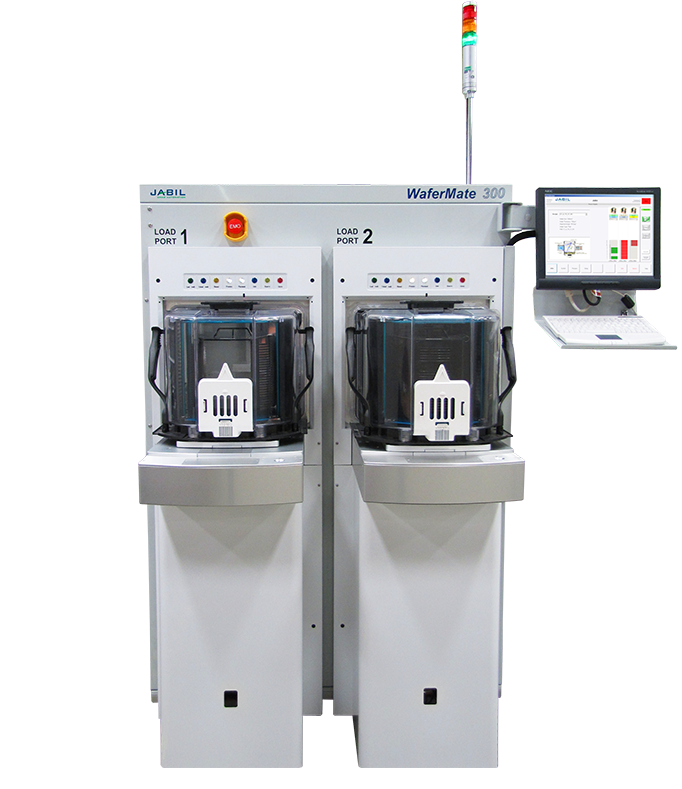
Key Features
-
Supports a wide range of wafer process tools & environments
-
Available in single and dual load port configurations
-
Can service up to 3 process tools at once
-
Adaptable for 200mm and smaller substrates
- Offering a range of end effector technologies - including vacuum, Bernoulli non contact, edge grip, and more
- Full safety guarding (OSHA and ANSI compliant)
- Cleanliness levels down to ISO Class-2
- CE, SEMI S2, and SEMI S8 Compliant
Available Accessories
- FOUP Opener
- SMIF Pod Opener
- Aligner
- Optical Character Recognition (OCR) Systems
- Barcode Readers
- Radio Frequency Identification (RFID)
- Ionization Bars
- Mini Environment
- Wafer Flip Module
- Pallet Transfer Station
- Wafer Conveyor / Oven Interface
- SMEMA & SECS/GEM Interfaces
WM300 Specifications | |
---|---|
Machine Footprint |
|
Wafer Alignment |
|
Wafer Placement |
|
Clean Room Classification |
|
Wafer Interface Options |
|
Cassette Positions Available |
|
Loadport Positions Available |
|
MTBF |
|
Compliance Standards |
|
Uptime |
|
Handling Capabilities |
|
WaferMate 200 Series Wafer Handling System
High-Performance Wafer Handling Automation Systems
The WaferMate200 is a high-performance wafer-handling platform, engineered for the expert automation of semiconductor wafers and similar substrates. The standard SMEMA interface provides the most cost-effective wafer-level process solution for systems that traditionally fit a conveyor layout.
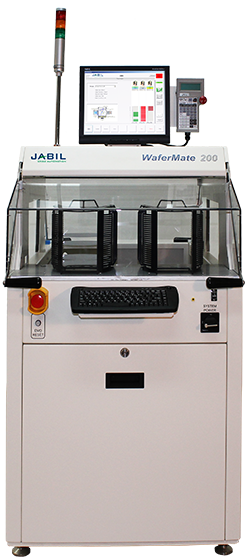
Key Features
- Pairs seamlessly with multiple types of process tools
- Configurable for two, three, or four cassette positions
- Suitable for all open cassette presentation formats
- Suitable for 50mm to 200mm wafers or 300mm from shipping cassette
- Can accommodate film frames, special thin and warped wafer components
- Full safety guarding (OSHA and ANSI compliant)
- Cleanliness levels down to ISO Class-4
- CE, SEMI S2, and SEMI S8 Compliant
Available Accessories
- Aligner
- Optical Character Recognition (OCR) Systems
- Barcode Readers
- Ionization Bars
- Mini Environment
- Wafer Flip Module
- Pallet Transfer Station
- Wafer Conveyor / Oven Interface
- SMEMA & SECS/GEM Interfaces
WM200 Specifications | |
---|---|
Machine Footprint |
|
Wafer Alignment |
|
Wafer Placement |
|
Clean Room Classification |
|
Wafer Interface Options |
|
Cassette Positions Available |
|
MTBF |
|
Compliance Standards |
|
Uptime |
|
Handling Capabilities |
|
Contact Us
Get in touch with one of our automation experts and see how we can help support your next automation project.
Ready to Automate?
Get in touch with one of our automation experts